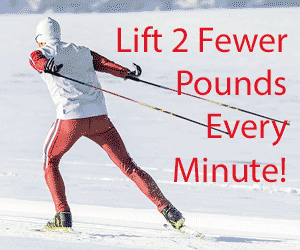
Skis are a complex and subtle assembly of a bunch of different materials, all of which react to heat differently. The structure or flex profile of the ski is formed by the interaction of structural layers or components which are bonded together using heat activated compounds. None of these components are inherently stable, and the bonding agents certainly seem to be vulnerable to overheating. These bonding agents reportedly are activated at about 70 degrees C. One would assume that once they've been activated and "set" that the bond is permanent. But the tendency of skis to move dramatically if they're left in the heatbox at or above 70 degree C would seem to indicate otherwise.
Leaving aside the structural assembly of the ski, and focusing on the base material, we've got another set of concerns. Most everybody has heard that base material can "burn", and that it happens at relatively low temperature. Well "burning" isn't quite so simple. The stuff starts to react, move and expand at about 120 degrees C. That reaction becomes more pronounced as temperature rises until it actually melts someplace up around 145 or 150 C. But inside that rather broad range there are a variety of semi-permanent and permanent transformations that fall short of melting but do alter the surface characteristics and density of the base material. It seems that temps of about 130C or above are capable of damaging the surface of the base.
Experiments on very thin sections (between 0.01 and 0.02mm) of base material (which I peel off the base with a metal scraper) have indicated that until the base material starts to actually react to heat on the order of 120 degrees C very little wax can penetrate or saturate the base. Once the base starts to expand then significant wax penetration is quite quick.
All of that information sets the stage for an examination of the type of damage we regularly see to skis when they arrive for grinding. Considering that we get to examine over 1000 pairs of used skis every season, we get a pretty representative sample of the types of abuse that skis are subjected to. When I first started working on skis I saw a huge number of "burned" bases. In the last couple of years I've become more sensitive to structural damage to the skis due to long-term exposure to moderate heat. It's not uncommon to find a ski that is wildly far from flat, but that has no significant hardening of the base material.
When I first started to recognize how many people were burning their skis I joined the chorus of professionals calling for much lower iron temperatures. However, I have since come to the conclusion that these low iron temperatures are forcing people to spend too much time ironing their wax, and they're therefore overheating the core of the ski.
Last year Nick Brown said something along the lines of "the less you work on your skis the faster they'll be". It certainly seems applicable under the circumstances. When we look at the act of ironing wax, there is a mighty fine line between burning the base and overheating core. Where does that leave you? We've all heard stories of World Cup technicians to just crank the irons all the way up and work really fast. While I wouldn't necessarily advocate that approach, I'd definitely suggest running an iron hot enough to ensure that the base is opening up, and that the wax is flowing quickly and easily. We want to keep the heat very local to the wax and the base. We're only going to get the wax a handful of hundredths of a mm into the base material. So a hotter iron running quickly seems to be the best approach, and is certainly the approach that I've gravitated toward in my own work.
For starters, I'd suggest using a minimum iron temperature of 120 degrees C, even with the softest waxes. I'm certain that there will be experts out there who will argue with me on that point. And I will readily concede that a much lower iron temperature can be used if the goal is simply to spread wax over the base. But it's quite clear that very little saturation occurs at temps below 120C. (One side note - clearly base saturation in the heatbox works quite differently than with an iron. In the heatbox the saturation is a function of time. This is why we use very long saturation periods - we've cooked skis for several days at times, and usually go for at least 12 hours.)
Most wax companies (I've just examined packaging from Swix, Star and Ski*Go) have extremely appropriate iron temperature recommendations for their glide waxes. But it must be understood that these recommendations are suitable based upon the expectation that the ironing will be done quickly and properly. Several passes from tip to tail with out stopping or reversing the direction of the iron will be sufficient to do the job.